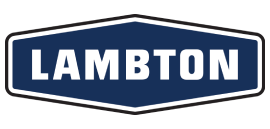
Bucket Elevator
Lambton’s bucket elevators are renowned for their superior quality and durability, thanks to the use of high-grade galvanized steel that ensures resistance to rust and corrosion, even in challenging agricultural environments. These bucket elevators are meticulously engineered to handle various grain types and capacities with ease, offering smooth and reliable operation while minimizing maintenance needs. Furthermore, Lambton offers a range of customization options for their bucket elevators, allowing operators to tailor the equipment to their specific needs. Options such as different bucket sizes, belt types, and elevator heights provide flexibility in installation and operation. This customization ensures that Lambton bucket elevators can be integrated seamlessly into existing grain handling systems or designed as part of new installations. Their commitment to innovation is evident in continuous advancements aimed at enhancing efficiency and safety, aligning with the evolving needs of modern agricultural practices.
Specifications
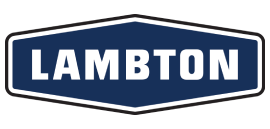
Level Chain Drag Conveyor
Lambton’s level drag chain conveyors represent a pinnacle of engineering excellence and operational efficiency in the realm of grain handling equipment. These level drag chain conveyors are engineered to handle varying capacities, with models capable of processing up to 30,000 bushels per hour (762 metric tonnes per hour). This high capacity ensures that Lambton level drag chain conveyors can efficiently transport large volumes of grain, supporting continuous flow and maximizing throughput during peak harvesting periods. The use of precision-engineered components, such as high-tensile strength chains and wear-resistant flights, ensures smooth and reliable operation, reducing downtime and increasing productivity. Their robust construction and durable components, including galvanized steel for enhanced longevity and corrosion resistance, ensure reliable performance even in demanding agricultural environments.
Specifications
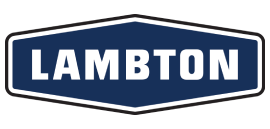
Round Bottom Drag Chain Conveyor
Lambton is dedicated to enhancing efficiency and cleanliness in grain handling operations, offering a specialized line of round bottom drag chain conveyors designed to optimize cleanout processes. These round bottom drag chain conveyors are engineered to handle capacities ranging from 1,000 to 10,000 bushels per hour (approximately 25 to 254 metric tonnes per hour), making them ideal for a variety of farm and commercial applications. The round bottom design of Lambton’s drag chain conveyors facilitates smooth and efficient movement of grain, minimizing residual material and ensuring thorough cleanout between batches.
Specifications
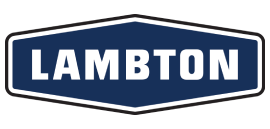
Incline Drag Chain Conveyor
When agricultural operations require efficient grain conveyance on inclines exceeding 10 degrees, Lambton excels with their specialized Incline Drag Chain Conveyor. Designed to handle steep inclines up to 45 degrees, these conveyors, also known as midpan or hy-flight conveyors, are engineered to meet the unique challenges of vertical grain transportation with precision and reliability. Lambton’s Incline Drag Chain Conveyor features a robust construction and innovative design that ensures seamless grain movement even in challenging terrain. The midpan or hy-flight configuration optimizes grain flow, maintaining steady movement while preventing spillage or backflow. This capability is crucial for applications where space constraints or terrain characteristics necessitate elevated conveying angles, such as grain storage facilities or processing plants.
Specifications
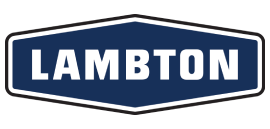
Incline Round Bottom Drag Chain Conveyor
Engineered to handle steep inclines of up to 45 degrees, these incline round bottom drag chain conveyors exemplify Lambton’s dedication to providing innovative solutions for grain handling challenges in agricultural and commercial settings. The Incline Round Bottom Drag Chain Conveyor is designed to ensure reliable performance and optimal grain flow dynamics on elevated terrains. Its round bottom configuration facilitates smooth movement of grain, minimizing friction and ensuring consistent material flow even at steep angles. The incline round bottom design of Lambton’s drag chain conveyors facilitates smooth and efficient movement of grain, minimizing residual material and ensuring thorough cleanout between batches.
Specifications
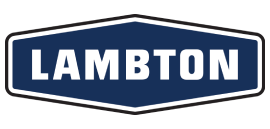
Double Run (Cannon) Chain Conveyor
Lambton’s Grain Cannon Chain Conveyor stands out as a highly versatile chain drag conveyor designed to handle material conveyance at steep angles of up to 60 degrees, utilizing a robust galvanized tube housing. This innovative conveyor offers a reliable solution for applications that traditionally necessitated augers or standard drag conveyors. What sets the Grain Cannon Chain Conveyor apart is its efficiency: it requires less horsepower and causes minimal damage to the conveyed material compared to augers, making it ideal for preserving the integrity of grains and other sensitive materials during transport. Lambton’s Grain Cannon represents a pinnacle of innovation in grain handling technology, offering agricultural professionals a reliable and efficient solution that enhances productivity, preserves product quality, and supports sustainable operational practices.
Specifications
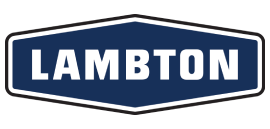
Loop Chain Conveyor
Lambton’s innovative grain loop chain system integrates several essential functions—truck receiving, conveying, bin unloading, and truck load-out—into a single, simple solution that offers convenience, efficiency, and cost-effectiveness for grain handling operations. Designed to streamline workflow and optimize space utilization, the grain loop chain conveyor is a versatile choice whether upgrading an existing site or integrating into a new grain handling system. By choosing Lambton’s grain loop chain system, agricultural professionals gain a reliable and integrated solution that enhances overall efficiency, reduces downtime, and maximizes the value of their grain handling investments.
Specifications
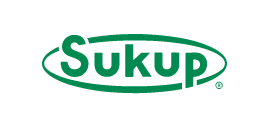
Bucket Elevator
Sukup bucket elevator’s are engineered with meticulous attention to detail, featuring UHMW seals on all shafts to enhance durability and minimize wear. The use of durable rubber belting and heavy-gauge trunking further reinforces their reliability, ensuring smooth and efficient operation even under demanding conditions. What sets Sukup Bucket Elevators apart is their versatility, offering a range of options tailored to handle various commodities effectively. Whether transporting grains, seeds, fertilizers, or other bulk materials, Sukup provides customizable configurations that meet specific application requirements. This flexibility allows agricultural professionals to optimize their grain handling processes while accommodating different operational needs and facility layouts. Beyond their technical specifications, Sukup Bucket Elevators are designed with user-friendly features that simplify maintenance and operation. This includes accessible inspection doors and strategically placed access points, facilitating routine maintenance checks and ensuring quick troubleshooting if needed. Operators can rely on Sukup’s elevators to deliver consistent performance, contributing to increased efficiency and productivity across grain handling operations.
Specifications
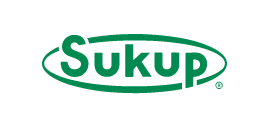
Level Drag Conveyor
Sukup Drag Conveyors stand out as a cornerstone of durability and customization in the realm of grain handling solutions. Crafted from heavy-gauge, galvanized steel, these level drag chain conveyors are engineered to withstand the rigors of agricultural and industrial environments, ensuring longevity and reliable performance over many years of operation. The galvanized steel construction not only enhances durability but also provides resistance to corrosion, making Sukup Drag Conveyors a reliable choice for handling various materials in diverse conditions. One of the key strengths of Sukup Drag Conveyors lies in their versatility and adaptability. Each conveyor system is customizable to fit specific operational and material handling requirements, offering flexibility in design and configuration. Agricultural professionals can tailor the conveyor’s dimensions, capacity, and features to optimize workflow efficiency and accommodate unique facility layouts.
Specifications
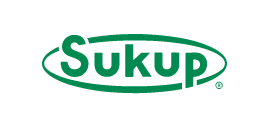
HY-Flight Drag Conveyor
Sukup Hy-Flight Drag Conveyors represent the pinnacle of innovation for agricultural operations requiring efficient material handling at steep inclines beyond the capabilities of traditional straight drag conveyors. These specialized conveyors are engineered to handle inclines up to 50 degrees, providing a versatile solution for navigating challenging terrain and optimizing space utilization in grain handling facilities. The key advantage of Sukup Hy-Flight Drag Conveyors lies in their ability to efficiently transport bulk materials at steep angles while maintaining smooth and consistent flow. This capability makes them indispensable for applications where space constraints or terrain limitations necessitate elevated conveying angles. By effectively managing material movement, Sukup Hy-Flight Drag Conveyors enhance operational efficiency and reduce the need for additional equipment or infrastructure modifications.
Specifications
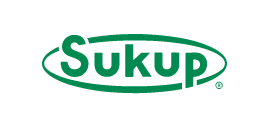
Double Run Chain Conveyor
The Sukup Double-Run Chain Conveyor stands out as a versatile and efficient solution in the realm of grain handling equipment, capable of replacing multiple traditional augers with its compact and innovative design. This conveyor system serves a variety of functions including replacing roof augers, transfer augers, grain dryer take-away augers, and even permanently installed transport augers. Its compact design not only saves space but also ensures smooth and quiet operation, minimizing disruption and enhancing operational efficiency. One of the key advantages of the Sukup Double-Run Chain Conveyor is its ability to handle grain with minimal damage compared to portable augers. This is crucial for preserving grain quality and reducing losses during handling and transport. The conveyor’s design ensures gentle handling of grains, maintaining their integrity and quality throughout the conveying process.
Specifications
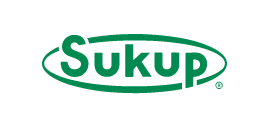
Chain Loop Conveyor
The Sukup Chain Loop Conveyor represents a comprehensive solution for grain handling operations, offering the versatility to perform multiple functions seamlessly within a single integrated system. This conveyor system excels in grain bin filling, unloading, blending, and transferring grain, streamlining operations and enhancing efficiency across agricultural facilities. The standout feature of the Sukup Chain Loop Conveyor is its ability to integrate various grain handling tasks into a single Loop Chain Conveyor. Whether filling grain storage bins, unloading trucks, blending different grain types, or transferring grain between different processing stages, the chain loop system ensures continuous and efficient operation without the need for multiple conveyors or additional equipment. This versatility not only optimizes space utilization but also reduces labor requirements and operational costs, contributing to overall operational efficiency and profitability.
Specifications
Bucket Elevators
RAD Bucket Elevators exemplify excellence in design and construction, offering agricultural operations a reliable solution built with top-quality components that ensure long-term performance and durability. Each bucket elevator system is meticulously engineered to uphold stringent standards, providing operators with dependable performance and maximum throughput while preserving the integrity of grains throughout the handling process. RAD Bucket Elevators are tailored to meet specific application requirements, offering customization options to suit various capacities and operational needs. Whether used for loading bins, conveying to processing systems, or transferring between storage facilities, these bucket elevators provide versatile solutions that integrate seamlessly into existing grain handling setups or new installations.
Specifications
En-Masse Drag Conveyor
RAD’s En-Masse drag conveyors stand out as robust solutions for efficiently moving bulk materials in agricultural and industrial settings. Designed with precision engineering and built using top-quality components, RAD ensures that every En-Masse drag conveyor delivers reliable performance and durability under demanding conditions. The design of RAD’s En-Masse drag conveyors is optimized for handling various materials with efficiency and minimal maintenance. These en-masse drag conveyors feature a robust chain and flight assembly that moves materials smoothly through the enclosed housing, reducing dust emissions and preserving the integrity of the conveyed material. This design not only enhances operational efficiency but also contributes to a cleaner and safer working environment.
Specifications
Round Bottom Drag Conveyor
RAD’s round bottom drag conveyors represent a pinnacle of efficiency and reliability in the realm of bulk material handling, particularly suited for agricultural and industrial applications. The design of RAD’s round bottom drag conveyors features a round bottom u-trough design, which facilitates smooth and efficient movement of materials such as grains, seeds, and other bulk commodities. RAD’s round bottom design of drag chain conveyors facilitates smooth and efficient movement of grain, minimizing residual material and ensuring thorough cleanout between batches. In addition to their operational benefits, RAD’s round bottom drag conveyors are designed with ease of maintenance in mind. Accessible inspection doors, strategically placed service points, and durable components simplify routine maintenance tasks and ensure minimal downtime for servicing.
Specifications
U-Through Screw Conveyor
The design of RAD’s U-Trough Screw conveyors features a U-shaped trough that houses a rotating screw mechanism. This configuration allows for efficient grain handling by providing a stable and contained pathway for bulk materials such as grains, seeds, fertilizers, and other commodities. In addition to their operational benefits, RAD’s U-Trough Screw conveyors are designed with ease of maintenance in mind. Accessible inspection doors, removable covers, and durable components simplify routine maintenance tasks and ensure minimal downtime for servicing.
Specifications
Incline Drag Conveyor
RAD’s Incline Drag Conveyors are engineered to provide efficient and reliable vertical or inclined movement of bulk materials, offering versatile solutions for agricultural, industrial, and commercial applications. These conveyors are designed with precision and durability in mind, utilizing robust materials and innovative features to ensure optimal performance in challenging environments. The design of RAD’s Incline Drag Conveyors includes a heavy-duty chain and UHMW paddle assembly housed within a sturdy casing. This configuration enables the conveyors to handle materials such as grains, seeds, fertilizers, and other bulk commodities with ease, even at steep inclines up to 45 degrees. The heavy-duty construction ensures durability and long-term reliability, making them suitable for continuous operation in demanding conditions.
Specifications
Double Run Drag Conveyor
RAD’s Double Run drag conveyors are designed to offer enhanced efficiency and versatility in handling bulk materials across agricultural and industrial applications. These drag conveyors are engineered with a focus on durability, reliability, and optimal performance, making them a preferred choice for operations requiring seamless material transfer and handling. This configuration optimizes throughput and minimizing material handling time. Whether used for loading bins, transferring between processing stages, or unloading trucks, the Double Run drag conveyor system streamlines workflow and enhances overall grain handling system efficiency.
Specifications
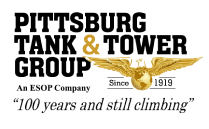
Bucket Elevator Support Tower’s & Catwalk’s
AllState Towers specializes in designing and manufacturing bucket elevator support towers and conveyor/man catwalks that play a crucial role in optimizing grain handling processes across various industries. These towers are engineered to support the weight and operational dynamics of conveyor systems, thereby enhancing reliability and safety in material transport operations.
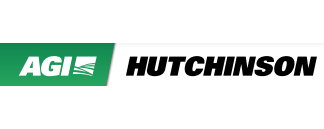
Grain Pump Conveyor (Loop Chain Conveyor)
AGI Hutchinson’s Grain Pump conveyor represents a cutting-edge solution in the realm of grain handling and material transport systems. This innovative conveyor system is designed to streamline operations by combining multiple functions into a single, integrated loop. The Grain Pump conveyor facilitates efficient handling of grain and other bulk materials throughout various stages of processing, from receiving and conveying to storage and load-out. One of the key benefits of AGI Hutchinson’s Grain Pump conveyor is its ability to significantly reduce labor costs and operational complexity. By automating material handling processes and integrating various functions into a single system, the Grain Pump conveyor enhances operational efficiency and reduces reliance on manual labor.